Cando se trata de fabricación, a tecnoloxía de mecanizado é un vínculo indispensable.O proceso de mecanizado é o proceso de conversión de materias primas na forma, tamaño e calidade de superficie necesarios, abranguendo unha variedade de métodos de mecanizado de precisión para satisfacer as necesidades de diferentes pezas.A continuación presentaranse en detalle 8 procesos de mecanizado comúns.
1. Xirando
O torneado é o proceso de xirar unha peza de traballo e usar unha ferramenta para cortar a superficie da peza para crear formas como planos, cilindros e conos.Este método de mecanizado úsase habitualmente para facer eixes, roscas, engrenaxes e outras pezas.Un torno é un equipamento común empregado para realizar operacións de torneado.
2.Fresado
O fresado usa unha ferramenta rotativa para cortar material na superficie da peza.Ao controlar o movemento da ferramenta pódense fabricar pezas con formas complexas como planos, superficies cóncavas e convexas e engrenaxes.O fresado inclúe fresado plano, fresado vertical, fresado final, fresado de engrenaxes, fresado de contornos, etc. Cada método é axeitado para diferentes necesidades de procesamento.
3.Perforación
A perforación é o uso dunha broca xiratoria para cortar material nunha peza de traballo para formar un orificio do diámetro e profundidade necesarios.É amplamente utilizado nos campos de fabricación, construción e mantemento.A perforación adoita dividirse en diferentes tipos, como a perforación convencional, a perforación central, a perforación profunda e a perforación en varios eixes.
4.Moenda
A moenda é o corte ou moenda gradual de material na superficie dunha peza mediante o uso de ferramentas abrasivas para obter a forma, tamaño e calidade de superficie desexados.A moenda divídese en moenda de superficie, moenda cilíndrica, moenda cilíndrica interna e moenda de contorno.
5.Aburrido
A perforación é un método de procesamento que usa unha ferramenta rotativa para cortar a peza de traballo para producir un burato circular ou outras formas.A perforación adoita usarse para procesar pezas grandes e pezas con requisitos de alta precisión, o que pode acadar un procesamento de alta precisión, alta calidade de superficie e alta eficiencia.O aburrido é amplamente utilizado na aviación, automóbil, fabricación de maquinaria e outros campos.
6.Planificación
O cepillado consiste en cortar material sobre a superficie dunha peza usando unha lámina de cepillado para obter a superficie plana desexada, dimensións precisas e calidade da superficie.O cepillado adoita utilizarse para mecanizar superficies planas de pezas máis grandes, como bases, bancadas de máquinas, etc. O cepillado normalmente divídese en dúas fases: desbaste e acabado.Durante a fase de desbaste, a cepilladora corta máis profundamente para eliminar o material rapidamente.Durante a fase de acabado, a profundidade de corte redúcese para conseguir unha maior calidade superficial e precisión dimensional.
7.Brochado
O ranurado usa unha ferramenta de ranurado para profundizar gradualmente o corte e crear contornos internos complexos.Adoita utilizarse para mecanizar formas complexas como contornos, sucos e buratos en pezas de traballo.A mergullo xeralmente pode acadar unha maior precisión de mecanizado e calidade de superficie, e é axeitado para pezas que requiren alta precisión e boa calidade de superficie.Xeralmente dividido en ranuras planas, ranuras de contorno, ranuras de ranuras, ranuras de buratos e outros tipos.
8.EDM
EDM utiliza descarga de arco para cortar e procesar materiais condutores para obter pezas de alta precisión e formas complexas, como moldes e ferramentas.Utilízase habitualmente na fabricación de moldes, moldes de inxección de plástico, pezas de motores aeroespaciais, equipos médicos e outros campos.A electroerosión adoita utilizarse para procesar materiais duros, fráxiles ou de alta dureza que son difíciles de cortar cos métodos tradicionais de mecanizado, como o aceiro para ferramentas, o carburo, as aliaxes de titanio, etc.
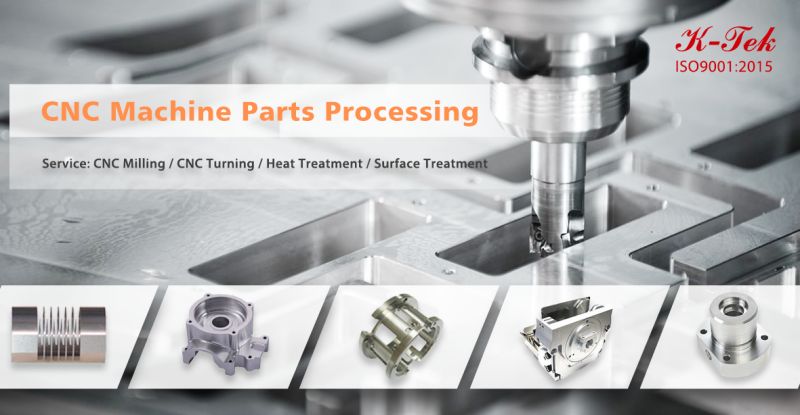
Hora de publicación: 19-12-2023